A type of pile, sheet, or spile, used as a column of the word steep or sometimes concrete to support a structure driving into the ground, is called sheet piling. Arther William (2021) defines Sheet Piling as a vertical interlocking system that creates a continuous wall. These walls are utilized to retain either soil or water. The significance or importance of sheet piling is immense, which are
- Provides high resistance to driving stresses.
- Lightweight.
- It can be reused on several projects.
- Provide a long service life with modest protection above or below water.
- Simple as well as easy to adapt the pile length.
Sheet Piling Could Be Your Construction Project’s Best Friend
Table of Contents
ToggleThe sheet piles are inserted into the excavation pit by crawler cranes, telescopic cranes, or duty cycle cranes using special vibration or pile-driving methods to a suitable depth and connection. Finally, they constructed a vertical wall called a sheet pile wall. This wall supports the soil as a shield by serving against water.
It can be used permanently or temporarily. Temporarily, the sheet is pulled by cranes from the ground. After completion, the sheet is pulled from the ground and laid down in a controlled manner. The sheet piles can then be reused. For various construction projects, Sheet piling is considered a crucial component because it provides stability and support to construction structures within challenging soil and water conditions.
To explore sheet pile driving methods, we will address common problems, present solutions, and demonstrate the materials used in sheet piling. We will also discuss their advantages, limitations, and the best uses for these materials. Let’s start with some common methods:
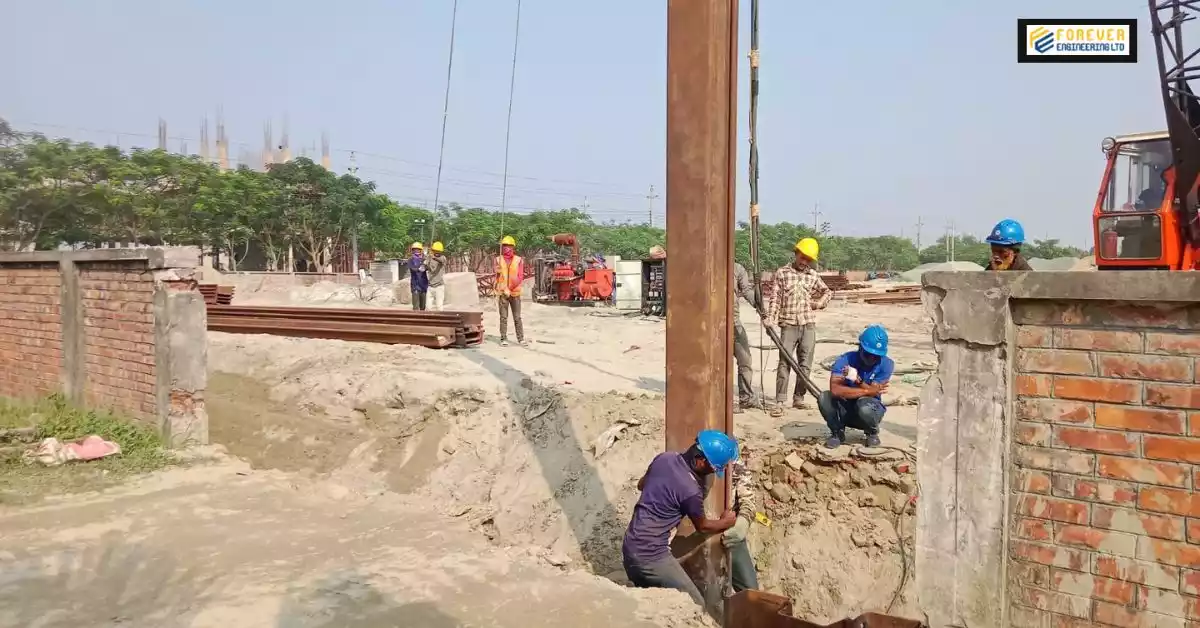
Impact Driving
An impact hammer is a specialty hammer that drives sheet piles into the ground. It consists of a heavy ram weight. This ram is raised mechanically or sometimes hydraulically to some height (termed “stroke”).
An impact hammer’s ram finally dropped onto the head of the pile. It has an apparatus that allows the ram to move quickly upwards, fall onto the driving system, and pile. During giving impact to the structure, the kinetic energy of the ram is converted into a pile. This finally causes the pile to penetrate the ground.
Vibratory Driving
A machine used to drive piles in/out of the ground to produce effective and strong structures like airports, bridges, or harbors is called the Vibratory Hammer. It is a mechanical sine-wave oscillator containing weights rotating in opposite directions.
The effect of the vibrations is an oscillating vertical force classified by frequency and amplitude. A vibratory hammer makes quick work of hammering into heavy or hard piles and increases efficiency on the job site. Vibratory hammers are used to drive in piles as well as extract them.
Processing Method
The processing of sheet poling consists of driving the piling of the second sheet pile into the ground and repeating till the installation of complete sheet piles. There are various noise control techniques available in construction engineering with wide applications. This noise control system provides substantial noise reductions. This technique also offers quick, low-cost solutions with no effect on operation. For example, Vibration damping, Vibration isolation pads, Fan installation and efficiency, Aerodynamic fan noise control – silencing without silencers, Pneumatic exhaust silencing, and many more.
Common Sheet Pile Driving Problems and Solutions
Problem 1: Obstructions in Soil
Sheet pile installation is difficult in soils with boulders or cobbles. In such a situation, the workers cannot easily reach the expected or desired wall depths.
Solutions
This problem can be reduced by using a hydraulic pressing method that jacks the piles into the required location. Another solution is pre-augering, using a more powerful hammer, or removing obstructions. This method is based on each pile using the previously installed one’s reaction force to push the pile into the ground.
Problem 2: Pile Refusal
Pile refusal makes mention of piles reaching their structural limits. It generally occurs between 10 to 12 blows within each inch. However, for practical pile driving, all piles must drive to an ultimate bearing resistance of 330 tons, called refusal. The capacity of the pile, at 330 tons (or 660 kips), is called a stout pile support system.
Solutions
This problem can be solved by Lifting and lowering the pile multiple times as the penetration becomes slower, which usually helps. Moreover, Changing the driving method, using a more robust pile material, or reassessing soil conditions can be solved.
Problem 3: Environmental Concerns
Sheet piling has environmental problems and negative effects, including noise, groundwater, soil disturbance, and vibration. For example, water ingress in marine structures and breaches in the piling can allow water to seep through—jeopardizing the entire purpose of the barrier. This can lead to soil erosion, flooding, or undermining adjacent structures.
Solutions
These issues can be resolved by making flood protection systems, recycling, and soundless mechanisms. Furthermore, it can be solved by Opting for vibration-free pressing methods, using sound barriers, and scheduling work during less sensitive times.
How to Drive Sheet Piles Effectively: Techniques & Tips
There are a few methods that can be applied to drive sheet piles:
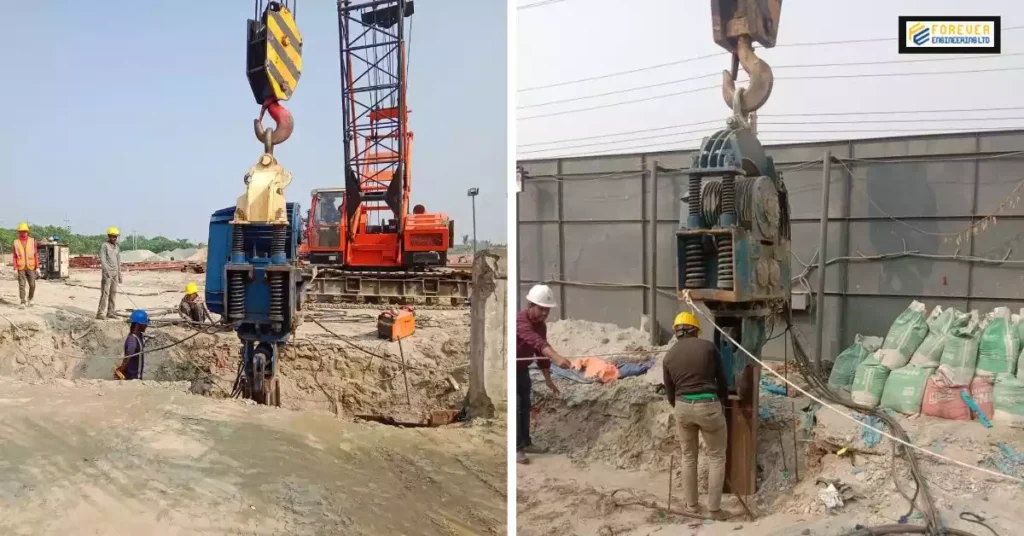
Driving Sheet Piles with Crane
Equipment Overview
An excavator or crane is needed to drive a sheet pile, and a hammer is required to extract a pile. Extraction is commonly used to recover steel -beams used in temporary foundation shoring. The pile-driving machine is positioned with an excavator or crane over the pile and is fastened to the pile by a clamp and bolts. While driving heavy or long piling sections, the crane boom length should be kept twice from the sheets.
Moreover, when installing the sheets, these should drive with the “male” interlock by leading into the soil. The engineer should consider driving sheets two-by-two, whenever possible, hammering the pair’s center as you go.
Advantages and Limitations
The advantages of using cranes in sheet piles include robust booms, low ground pressure thanks to wide track undercarriages, and the realization of customized special solutions. Nevertheless, installing it with a crane is difficult in soils with boulders or cobbles. It caused soil erosion and flooding by extracting groundwater.
Best Practices:
- Keep the length of your crane boom twice that of your sheets.
- Work only with undamaged sheets and check the quality of your soil.
- Remove debris from the site of installation.
- Utilizing high-strength jetting pipe to support pressing sheet piles within difficult ground conditions.
- Ensuring that the piles are installed as per the correct alignment.
Driving Sheet Piles with an Excavator
Equipment Overview
Sheet pile driving equipment is required to drive the sheet pile into the ground. Here, an excavator is a significant piece of equipment. Utilizing an excavator-mounted pile driver is one of the best ways to improve your bottom line and ensure efficiency on any pile-driving project.
Excavator-mounted vibro hammers also allow operators to lower their transportation costs, which include variable costs like fuel. Side grip vibrio hammers mounted on an excavator can load, unload, and extract piles while offering 360° of rotation and are designed for extended, continuous use associated with larger-scale projects with crews working in shifts. This increases the overall construction productivity and reduces overall construction costs. Thus, it helps keep the project on schedule.
Advantages and Limitations
The use of an Excavator in sheet pile diving gives strong production capacity, the production of excavators with high yield and high efficiency, coupled with Wuxi Beiyi machinery for the direct sales of the manufacturers, manufacturers’ independent research and development, and sales, why the method is cost-effective. However, the negative side of it is that the sheet pile section and interlocking elements dictate excavation shapes. Moreover, neighborhood disturbance can be caused by Sheet pile driving.
Best Practices
- A guide structure or templates need to be used to ensure that piles are placed and driven within the exact alignment.
- At least two templates can be used to drive each sheet pile or pair of sheet piles recommended by driving constructors.
- Templates should also be used to obtain the proper plumpness of the sheet pile wall.
Driving Sheet Pile with Diesel Hammer
Equipment Overview
Diesel pile hammers are heavy-duty machines that drive large steel, wood piles, or concrete within the ground. Diesel hammers do not use crankshafts, piston rods, cams, or bearings, reducing the hammer’s overall wear and tear. Moreover, the other equipment for pile driving includes the pile hammer, the vibro hammer, the sheet pile hammer, and the hydraulic sheet pile driver.
The diesel impact hammer operates in four phases: The ram is raised, and fuel is injected. Compression: The ram is released and free-falls. The closure of the exhaust port finally compresses the air and fuel together.
Advantages and Limitations
Diesel hammers are fuel-efficient and self-contained. The advantage of it is that it requires and burns less fuel compared to others, which means ensuring bottom-line savings. Moreover, they are self-contained. This means that these do not require any external power supply.
The hammer efficiency is set for all diesel hammers to 0.8, meaning roughly 20% of the ram’s energy is lost due to some unknown reason before impact. Nevertheless, Diesel impact hammers with higher impact velocity are commonly considered more suitable for steel piles driven to a high capacity. However, the hydraulic hammer’s lower impact velocity is traditionally deemed more appropriate for concrete piles, which is its limitation.
Best Practices
To optimal use and ensure the longevity of the equipment, some actions should be followed which are:
- In terms of keeping machinery as close to upper-level performance as much as possible using Scheduled preventative maintenance.
- The company can avoid this problem by training employees to properly use each piece of equipment during their workday.
- Regular cleaning helps operators avoid different problems and offers the opportunity to inspect the components inside the machine for signs of fatigue or premature wearing.
Frequently Asked Questions (FAQ’s)
Sheet piles are primarily made of steel, but they can also be crafted from vinyl, wood, or reinforced concrete, depending on the project requirements and environmental conditions.
The depth to which sheet piles can be driven varies based on soil conditions, the type of sheet pile, and the equipment used. Typically, they can be driven up to 30 meters (about 100 feet), but deeper installations are possible with specialized equipment and techniques.
The choice between a vibratory hammer and an impact hammer depends on soil composition and project specifications. Vibratory hammers are preferred for softer soils where less force is needed, while impact hammers are used in denser soils that require more force to penetrate.
Misalignment can often be corrected by applying lateral forces to adjust the position of the piles or by using guiding templates during installation. In some cases, partially driving the piles and then realigning before final installation is necessary.
Key safety precautions include wearing appropriate personal protective equipment (PPE), ensuring all machinery is in good working order, maintaining a safe distance from operating machinery, and adhering to established safety protocols and guidelines to prevent accidents.
Conclusion
The article successfully represents How to Drive Sheet Piles: Methods, Problems, and Solutions to help the scholar learn the sheet piles and create an in-depth understanding.
At Forever Engineering Ltd, we’ve mastered the art of driving sheet piles, ensuring each construction project stands on firm ground. Our expert team handles challenges like soil obstructions and environmental concerns with innovative solutions, employing the latest techniques for efficiency and minimal impact. From cranes to vibratory hammers, we use top-notch equipment, always prioritizing safety and environmental sustainability.
Our commitment to excellence and seamless execution makes us leaders in the construction industry, delivering projects that are not only durable but also eco-friendly. Trust us to lay the foundation for success in every endeavor.